Process Deposit Build-up Control
Finally, a process friendly Solution to your Plant’s
Process Deposition Problems !
Reduction of Plant Downtime.
Improvement of Plant Efficiency.
Reduction of Energy Costs.
Effective On-line Maintenance.
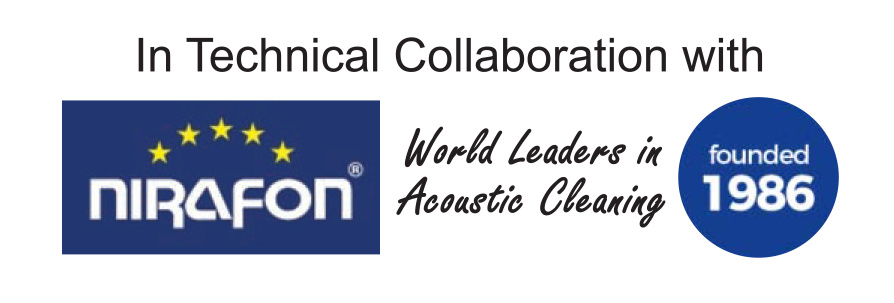
The first step to tackle process deposits affecting Heat Transfer, Pressure Drops,  Material Flow and Equipment Vibration is to disrupt the build-up at frequent intervals…
The second step –Â to disrupt in an on-line and process friendly manner which is the reason why Nirafon Acoustic Cleaning is the best bet for such a challenge!
f.harley
Process Deposits Build-up Control
F. Harley in technical collaboration and financial partnership with Nirafon Oy, Finland in 1995 formed
Harley Nirafon India Pvt. Ltd., and introduced the Acoustic Cleaning or Sonic Cleaning Systems to India.
Harley Nirafon India Pvt. Ltd. successfully introduced the systems in the Indian Market, across a wide spectrum of applications and industries and continues to do so under technical collaboration with Nirafon Oy, Finland, now through its parent company F. Harley.
our services
Technical Research
Acoustic Cleaning or Sonic Cleaning has been used successfully for more than a decade in the U.S. and Europe, and the technology behind the Company & products is a result of Nirafon Oy & dose and ongoing co-operation with research institutes and universities, notably the prestigious Helsinki University ofÂ
Technology and VTT Technical Research Center of Finland.
Backed by the continuous research and product development of Nirafon Oy, Finland, F.Harley under the ongoing technical collaboration has a firm background in producing practical solutions in the area of Acoustic Cleaning.
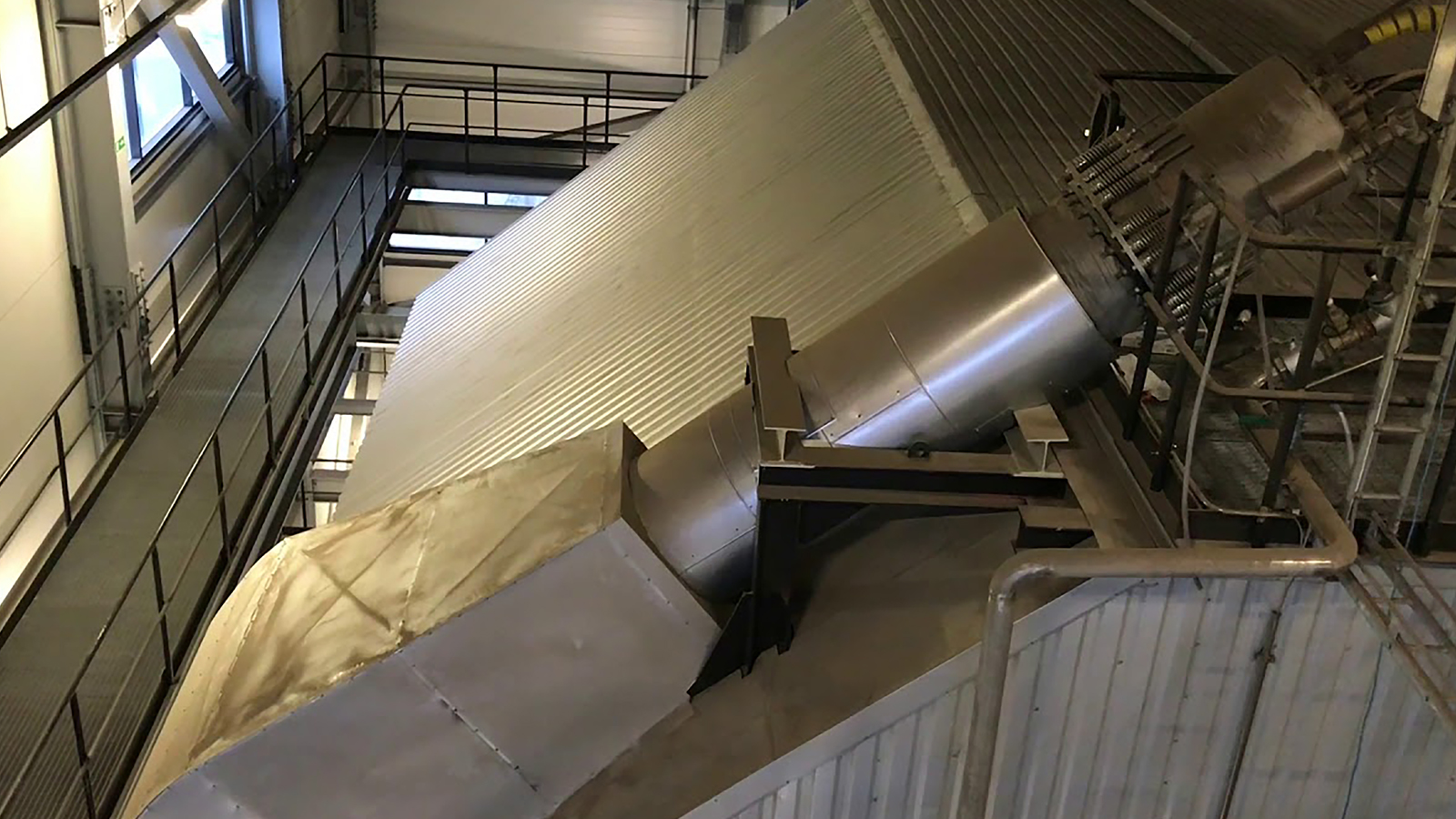
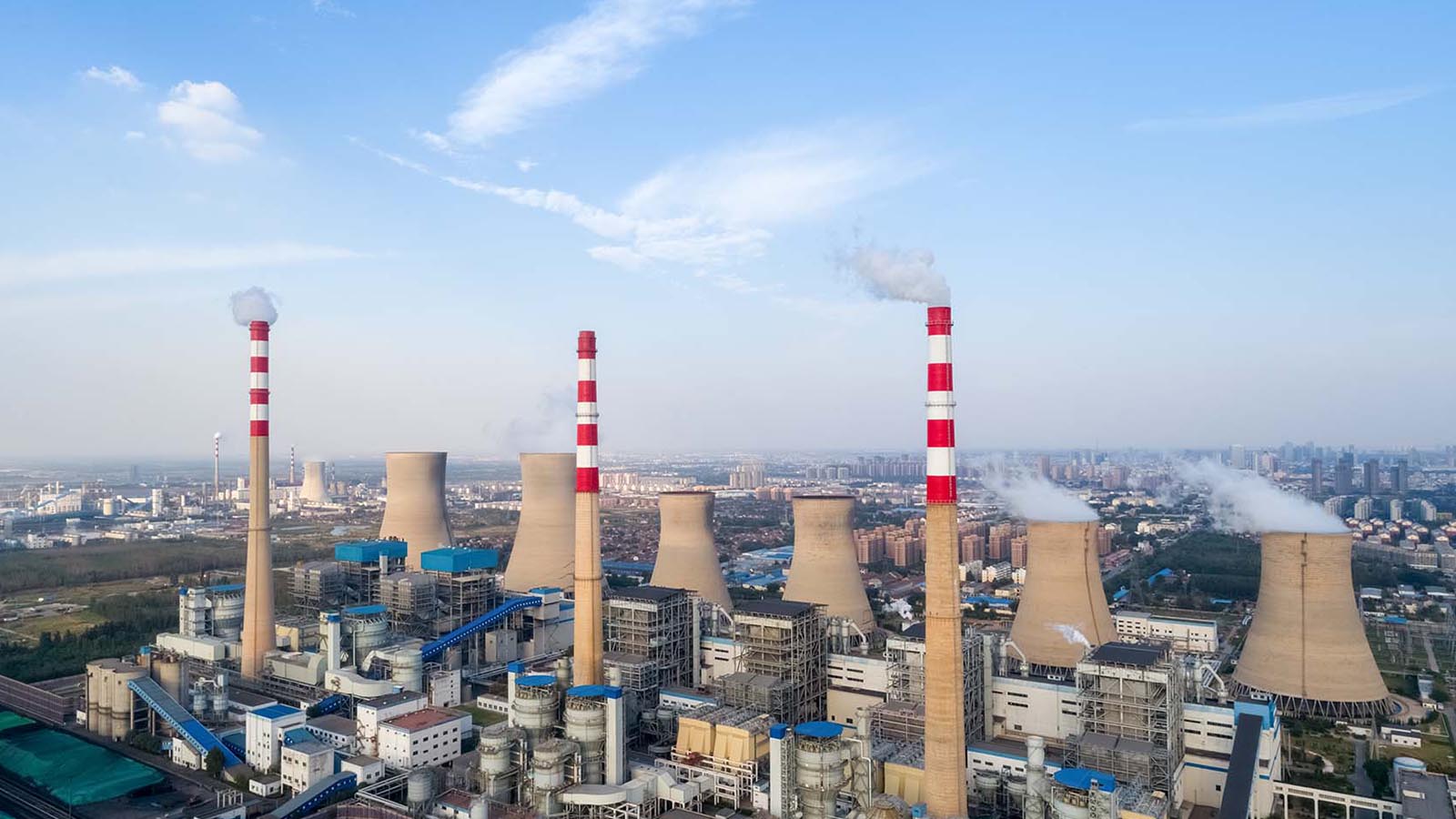
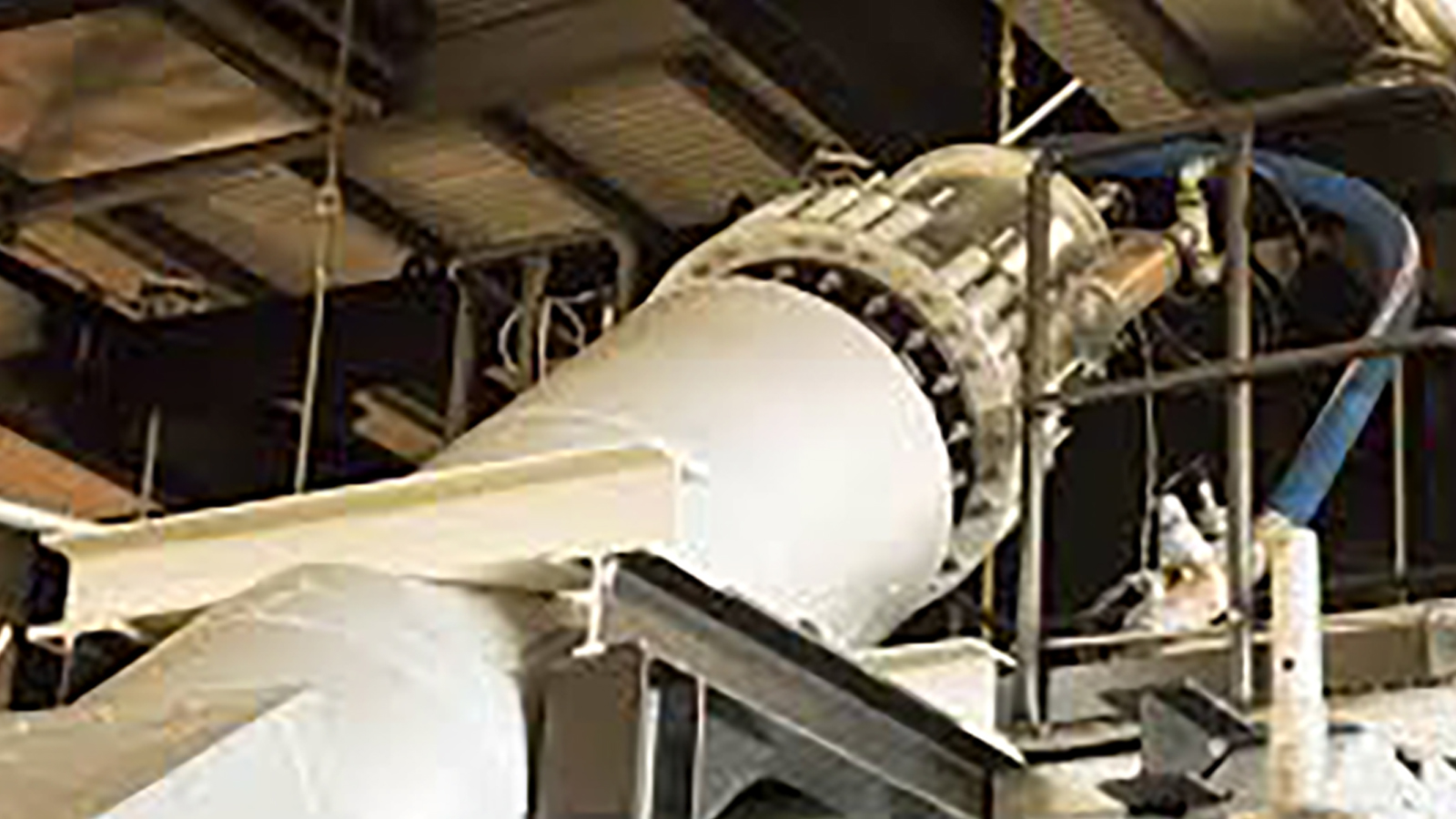
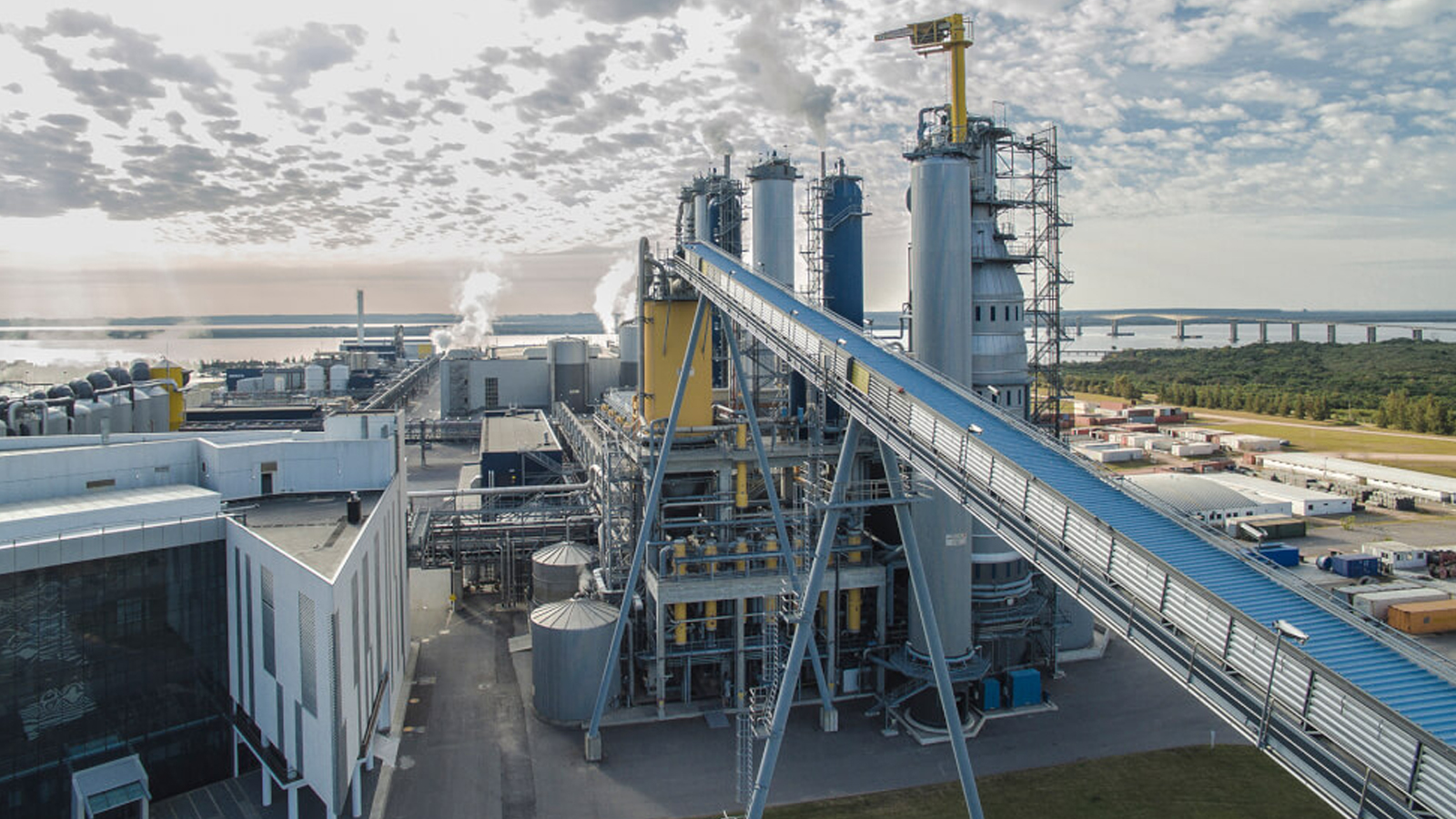
Nirafon
Acoustic Cleaning Process
Ash, soot and particulate build-up problems have always been associated with creating challenges affecting Heat Transfer, Pressure Drops, Material Flow and Equipment Vibration in processes, thus posing severe operational and maintenance problems.
The Nirafon Acoustic Cleaning Process is just that solution which with its unique on-line operation is found to be the most process friendly and effective method of cleaning for the following reasons
A. Traditional Cleaning Methods causing damage to Equipment Parts and Components i.e.
- tubes corrosion and erosion through steam soot blowing operation in Boilers,
- filter bags mechanical stress through pulsing mechanism in Bag Filters,
- equipment / structural damage caused by manual poking and hammering or even Mechanical Vibrators in Hoppers etc.
The prime reason for causing damage to the process parts and equipments is due to excessive stress caused due to the very inherent aggressive nature of these cleaning methods, and the fact that it is mostly and the only cleaning method employed in absence of a better alternative which can deliver same or even better results, and without causing damage to equipment part damage.
Furthermore, while these traditional and aggressive cleaning methods may be required for the expulsion of the build ups across a fixed time duration, the process friendly Nirafon Acoustic Cleaning System helps in the removal of build ups between these fixed time durations and helps gain better control over the rate of deposit build up over time. This also results in relying less on the traditional cleaning systems, and in some cases also replaces the traditional systems as well.
B. Ineffective cleaning by Traditional Cleaning Methods i.e.
- steam sootblowers in Boilers SCR’s due to localized cleaning and extreme maintenance issues,
- ineffective pulsing mechanism resulting in practical blinding of filter bag bottom,
- undetectable deterioration in mechanical rapping system in ESP’s unless increase in emissions,
- ineffectiveness of air blasters in fans / blowers hindering control over equipment vibration and
- manual vibrators / manual poking hammering in hoppers, bins and silos causing equipment and structural damage.
C. No Mechanical In-Situ Cleaning Solutions applied or available i.e.
- in Forced Draft Coolers and Heat Exchangers causing fouling within the tubes and not addressed till manual cleaning is performed,
- for fan / blower applications affected with vibration problems no solution is applied as air blasters are not acceptable due to the fact they inject a thrust force upon the impeller, thus requiring frequent shutdowns and manual chipping of the hard deposits
over the impeller, - in Spray Driers, Cyclones and Ductlines there are no solutions which prevent side wall build ups which would help both material flow and control pressure drops.
While industry has been tackling this process build up and deposits problem for the many years with traditional cleaning methods, it is observed that these methods fall short in providing a balanced solution from the viewpoint of investment, performance, effectiveness, operation as well as maintenance convenience and costs. On the other hand, the Nirafon Acoustic Cleaning Process emerges as a cost effective, economical, user and a process friendly solution in dealing with process build ups and deposit challenges in temperature environments ranging from Ambient to 1500°C, across a wide range of applications.
Nirafon
Acoustic Cleaning Process
Nirafon Acoustic Cleaning
System up to 1000°C
Nirafon Acoustic Cleaning Systems utilise the energy in the low frequency sound waves (60-250Hz) generated by a pneumatically operated Acoustic Horn. This energy resonates and dislodges dust, soot or other particulate matter which tends to deposit on various surfaces of industrial equipment.
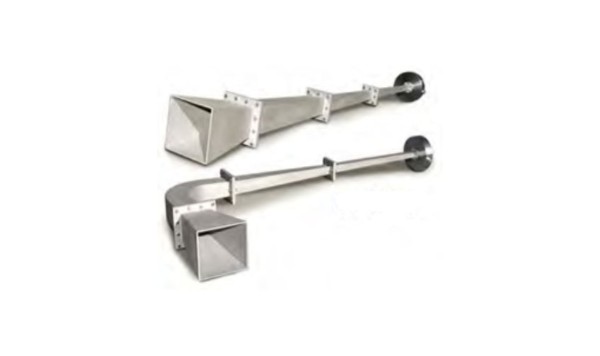
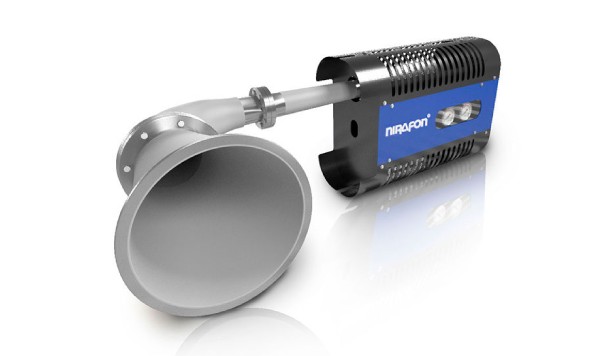
Nirafon Sound Cleaning
Device up to 1500°C
Specially designed for cleaning of high temperature areas, up to 1500°C flue gas temperatures Nirafon Cleaning Sound Device is an effective non-invasive method for cleaning of the high temperature areas of the boiler plants. The method enables the on-line cleaning of both the furnace area…
Advantages of Nirafon Acoustic Cleaning Methods
The Nirafon Acoustic Cleaning Process comprising of the Nirafon Acoustic Cleaning Systems (Sonic Horns) as well as the Nirafon Cleaning Sound Device offer several distinct advantages as a superior and cost effective alternative to conventional cleaning methods:
1. Cleaning is possible in inaccessible places !
Unlike conventional cleaning methods which provide localised cleaning, Nirafon Acoustic Cleaning Systems use sound waves which travel in three dimensional space to reach even inaccessible places for effective cleaning.
2. Maintains plant efficiency at a high level !
Nirafon acoustic cleaning continuously removes soot, ash and particulate matter deposits from surfaces, thus preventing formation of build ups, thereby maintaining heat transfer efficiency in Boilers, pressure drops in Bag Filters, vibration levels in Fans etc. at desired levels.
3. Cleaning without interrupting plant process/production !
Nirafon acoustic cleaning is a totally independent process which does not require stoppage or interruption of production. Being an on-line process, it significantly reduces or even eliminates down time and increases equipment availability. At the same time, Nirafon Acoustic Cleaning Systems can be used during plant
shutdowns to minimise requirement of manual cleaning.
4. Cleaning without damaging !
Conventional cleaning methods such as Steam Soot Blowing in Boilers are known to cause erosion to the heating surfaces leading to their premature failure. Similarly, manual hammering of walls causes damage to hoppers, bins, and cyclones while excessive use of compressed air pulses in bag filters causes high mechanical fatigue to the fabric leading to premature failure of filter bags. The Nirafon Acoustic Cleaning Systems perform the cleaning operation gently without causing damage, thereby enhancing the life of the mother equipment.
5. Lower initial capital investment !
When compared with traditional alternatives such as steam soot blowers for keeping the heating surfaces of the boiler clean, the Nirafon Acoustic Cleaning System as well as the Gas Pulse Cleaning System offer an extremely cost effective solution from the viewpoint of capital cost.
6. Lower operating costs !
Nirafon Acoustic Cleaning Systems require compressed air for their operation leading to much lower operating costs compared to traditional cleaning systems such as steam soot blowers which consume substantial quantities of steam having significant cost implications. Also power consumption by Nirafon Acoustic Cleaning Systems is minimal compared to conventional cleaning methods.
7. Lower service & maintenance costs !
Having minimal moving parts, Nirafon Acoustic Cleaning Systems require negligible maintenance, service and spare part costs.
8. Lesser space requirement !
Nirafon Acoustic Cleaning Systems are compact and occupy much less space compared to conventional cleaning devices such as Long Retractable Soot Blowers. This adds further to the cost effectiveness of the Nirafon systems.
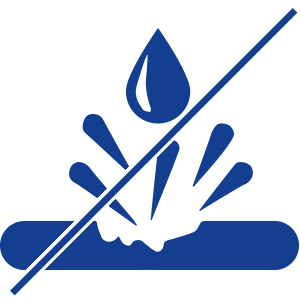
No water, no erosion,
corrosion or mechanical wear
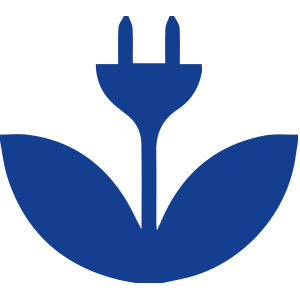
The most energy-effecientÂ
cleaning solution
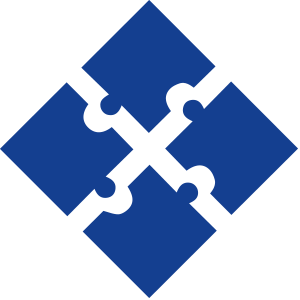
Customized solutions for
optimized results
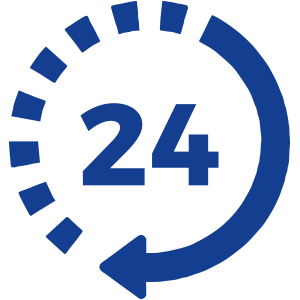
Cleanliness maintained
constantly
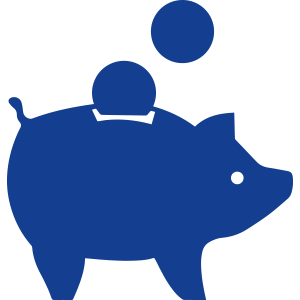
Bringing substantial
cost savings
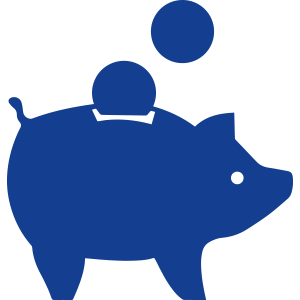
Process Friendly
F.A.Q
Frequently asked Questions
Nirafon Acoustic Cleaning
Process – a broad overview
How does Acoustic Cleaning Work?
Acoustic cleaner causes a sound pressure pulse which will detach the particles from the surfaces. The deposits adhering to the surface are subjected to a force greater than that retaining it. The particles with different masses are subjected to lternating sound waves. Because the particles have different masses, the distance they travel is a little different. When the sound impact is repeated with appropriate frequency the particles go out of phase with each other and break apart. The required frequency of impacts depends on the amount of deposits, their natural vibration frequency and adhesiveness. When the impact on the deposit is frequent enough, the deposit comes off and the surface is clean.
How does Acoustic Cleaning Work?
Acoustic cleaner causes a sound pressure pulse which will detach the particles from the surfaces. The deposits adhering to the surface are subjected to a force greater than that retaining it. The particles with different masses are subjected to lternating sound waves. Because the particles have different masses, the distance they travel is a little different. When the sound impact is repeated with appropriate frequency the particles go out of phase with each other and break apart. The required frequency of impacts depends on the amount of deposits, their natural vibration frequency and adhesiveness. When the impact on the deposit is frequent enough, the deposit comes off and the surface is clean.
What kind of maintenance do the Acoustic Cleaning require?
Compressed air driven acoustic cleaners do not need a lot of maintenance. However, the maintenance is very important to the best efficiency of the cleaner. When the membrane of the generator is worn it has to be turn over or changed. If the sound pressure of the cleaner decreases 3 dB the sound power level is cut to half. The generator contact surfaces also have to be re-machined. This does, however, not have to be as frequently as the change of membrane. NSCD® doesn’t also need a lot of maintenance. The condition of the gas valves and all the gaskets have to be regularly checked and the igniters have to be change in a certain period of time.
What is the outside noise level caused by Acoustic Cleaners?
The outside noise level caused by acoustic cleaner depends on the structures where it is installed. When installed to boiler wall the outside noise level is around 100 dB. The outside noise level of Nirafon NCSD does not exceed 85 dB and is not disturbingly audible outside the boiler.
Can the outside noise level be reduced somehow?
The outside noise level can be reduced to under 85 dB measured from one meter distance of the generator by using a proper sound insulation box. Nirafon can provide these boxes or instructions and drawings to make proper sound insulation boxes. The effect of the sound insulation boxes is, however, not the same if there are some openings in the walls of the applications the cleaners are installed or it is not sufficiently insulated.
What is the maximum temperature for Horn Materials?
Nirafon horns are made of SS2342 (AISI316) acid proof steal and in the higher temperature areas the mouth cone of the horn is usually made of G-X15-CrNiSi229. These materials can take the temperatures up to: SS2343 c. 1000ËšC and G-X15-CrNiSi229 c. 1050ËšC. The materials can take these temperatures in conditions where oxygen is present. The conditions where the horns are located oxygen is not usually present and the materials can take even higher temperatures. Also the horn is usually installed into an opening in membrane wall and the temperature near the wall is not as high as it is further away from the wall. At Helsinki Energy Salmisaari power plant in Helsinki Finland the horns are located in a temperature area of 1400 degrees Celsius and have been there since 1999 and the mouth cones of the horn inside the boiler are still in perfect condition.
What is the principle of the Nirafon Acoustic Cleaning Process?
Nirafon Acoustic Cleaning Systems utilize the acoustic energy of low frequency sound waves, which are generated in form of acoustic pressure pulses. These pressure pulses weaken the bonds between the particles themselves as well as between the particles and the surface. This causes the bonds to break and the particles are dislodged from the surface to which they were adhering. The dislodged particles are carried away by air/ gas stream or by gravity.
Nirafon Acoustic Cleaning
Systems – pneumatically operated up to 1000°C
How does Acoustic Cleaning Work?
Acoustic cleaner causes a sound pressure pulse which will detach the particles from the surfaces. The deposits adhering to the surface are subjected to a force greater than that retaining it. The particles with different masses are subjected to lternating sound waves. Because the particles have different masses, the distance they travel is a little different. When the sound impact is repeated with appropriate frequency the particles go out of phase with each other and break apart. The required frequency of impacts depends on the amount of deposits, their natural vibration frequency and adhesiveness. When the impact on the deposit is frequent enough, the deposit comes off and the surface is clean.
Can existing build-ups/ depositions which have become hard be cleaned by using NACS?
Acoustic Cleaning Technology is based on the Preventive Maintenance philosophy. It is always recommended that before NACS is installed for any application, the equipment surfaces facing deposition problems be cleaned thoroughly so that NACS can work on clean surfaces and prevent the dust particles to build up and develop into a solid hard mass. It is difficult to remove already formed hard/solid deposits by using NACS. However, it is possible to remove existing accumulations of loose dust/ash by using NACS.
What does the total hardware comprise of?
Compressed air driven acoustic cleaners do not need a lot of maintenance. However, the maintenance is very important to the best efficiency of the cleaner. When the membrane of the generator is worn it has to be turn over or changed. If the sound pressure of the cleaner decreases 3 dB the sound power level is cut to half. The generator contact surfaces also have to be re-machined. This does, however, not have to be as frequently as the change of membrane. NSCD® doesn’t also need a lot of maintenance. The condition of the gas valves and all the gaskets have to be regularly checked and the igniters have to be change in a certain period of time.
What is the power requirement for operating NACS?
Since there are no electrically driven moving parts, NACS has very low power consumption. Solenoid valves (8-10W each) are required to be operated intermittently using the ECU. The Power supply to the ECU may be 220V AC/ 110V AC/24VDC as per client’s requirement.
What is the quality of compressed air required for operating NACS?
The compressed air should be free from dust, moisture and oil content. In case there is high moisture content in the compressed air, the client should provide air dryer or moisture trap to ensure moisture-free air for NACS. In most cases, plant air is quite acceptable for NACS operation, otherwise instrument air is used.
What is the air quality requirement for Acoustic Cleaners?
The acoustic cleaner uses normal work air. The valve group of the cleaner has a filter/water separator to take out the impurities and water out of the work air.
Nirafon Cleaning Sound
Device – gas operated up to
1400°C
How does Acoustic Cleaning Work?
Acoustic cleaner causes a sound pressure pulse which will detach the particles from the surfaces. The deposits adhering to the surface are subjected to a force greater than that retaining it. The particles with different masses are subjected to lternating sound waves. Because the particles have different masses, the distance they travel is a little different. When the sound impact is repeated with appropriate frequency the particles go out of phase with each other and break apart. The required frequency of impacts depends on the amount of deposits, their natural vibration frequency and adhesiveness. When the impact on the deposit is frequent enough, the deposit comes off and the surface is clean.
What kind of gas does the NCSD® use?
The NCSD® uses LP gas usually propane. The supply pressure of the gas is 2…4 bar
What is the air and gas consumption of NCSD®
NCSD® can make 1…15 pulses per second. One pulse uses about 0.4g of gas per pulse. In addition NCSD® uses circa 80 Ndm3 of compressed air while running for burning air and cooling
n case of gas leakage in NCSD®, can there be an explosion inside the boiler causing risk to the boiler structures?
When the NSCD® is operating the controlled explosions happen inside the combustion chamber of the cleaner. If, however, there is a gas leakage in the gas valves and the gas gets into the boiler, the amount of gas will be very small and will only burn inside the furnace causing no risk of explosion. It is not possible to big amount of gas getting into the boiler rapidly causing the risk of explosion. The pressure of the controlled explosion inside the combustion chamber is around 5 bar. Nirafon always supplies a strength calculation report of the combustion chamber with the NSCD®. In some cases the gas pulse cleaners have been working since 1999 and no signs of explosions inside the furnace have been detected.